
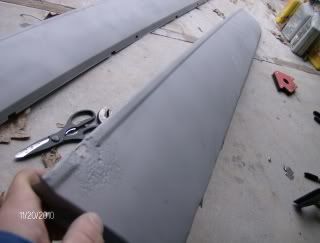
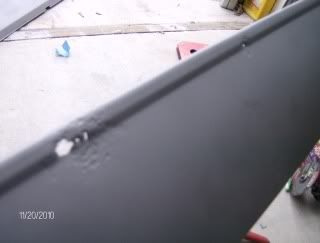
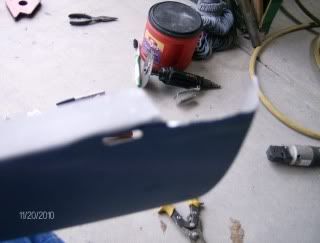
You can see the rust out areas. I cleaned up the end because the metal was very thin there. I'm going to make a piece to bend and weld into the corner. It has to bend around the back and have the bolt that connects to the car. This might take you a couple of times to get right. Just don't get discouraged. I will be using a welder, hole punch, panel flanger, throatless shear, die grinder, and needle nose pliers, and a piece of copper to do this job. If you don't have all this, don't worry I've done similar before with far less. You will need a welder though.
The first thing I did was go to the good panel. I used a piece of paper to copy the end that was missing. I even copied along the top of the panel a little further to insure I was going to have the correct angle of the end. I flipped that upside down and that will be the pattern for the missing part.
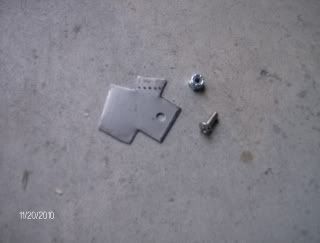
Before I could bend it. I punched a hole in it for the bolt. Put the bolt in and weld it. You can see the dotted line which represents the area that needs to be flanged. This whole piece will sit behind the panel except for the top which will sit level. Take your time and weld it. Don't have your welder set to high. You'll burn through it. I did this on #1 power.
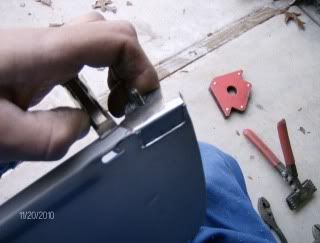
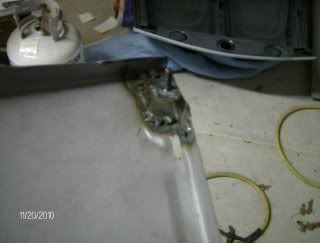
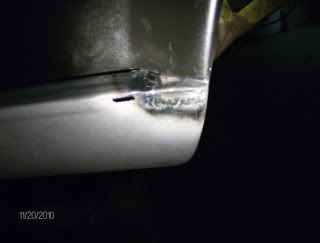
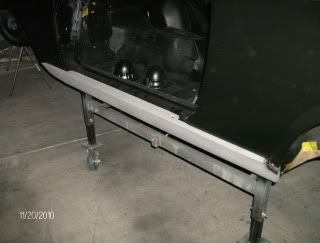
It looks good and the fit is perfect. Now back to fixing the holes in the panel. You could weld a piece of metal behind the hole. That could trap moisture later though. Take a piece of copper. Put it behind the hole. I used a magnet to hold it there. Your weld won't stick to the copper. Weld the hole shut. Grind off any excess and remove the copper from behind. Take your die grinder or sand paper and clean up the back too. You want the whole piece clean when you paint it. The next step for me is to paint the entire panel with epoxy primer. It is a self etching primer and contains zinc phosphate as a corrosion inhibitor. After I paint it (2 coats), I will do the body work. You want to paint the panel first to seal it. After the body work, I will paint it again two coats of epoxy with a reducer to get it ready for the base. I hope this was helpful. The panels we have on our cars now are much better than the ones you can buy. And if they're on your car, you'll know they'll fit.

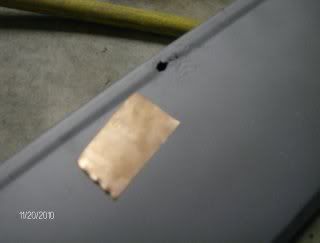
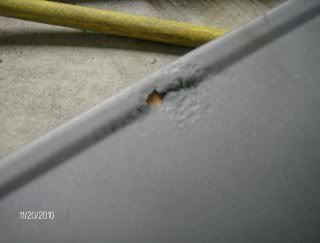
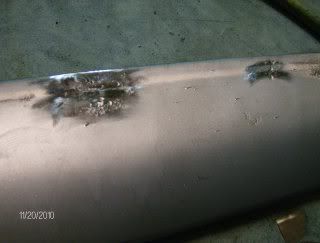
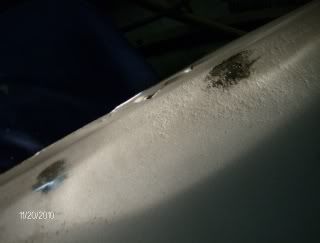
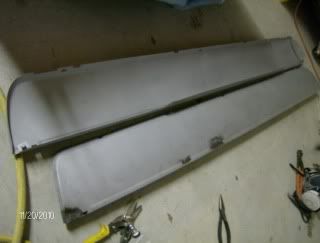